June 25, 2024
A Practical Guide to Logistics: The 7 Rights
There have been many years now since logistics became the backbone of commerce, ensuring products move smoothly from manufacturers to retailers to consumers. The complexity of this task requires careful organization and precision, guided by the principle of the 7 R’s, seven rights to aim for efficiency: Right Product, Right Quantity, Right Condition, Right Place, Right Time, Right Price, and Right Customer. Here are some practical guidelines on how these principles can optimize your supply chain and last-mile operations.
The Right Product
Delivering the right product is the cornerstone of logistics. It involves ensuring that the specific products a company can handle are delivered as required. Depending on the nature of the product, logistics and supply chain strategies must be adjusted. For instance, perishable items like food require refrigerated transport, whereas fragile goods need special packaging or white glove services. The more components involved in a delivery, the more complex the process becomes, demanding precision and careful planning to maintain efficiency and reliability.
Last-mile white glove services provide a premium delivery experience, handling products with extra care, setting up, and even assembling items for final users. This service is especially significant for high-value or fragile goods. Our white-glove services differentiate themselves by providing a superior customer experience, ensuring products arrive in optimal condition and are ready for immediate use.
The Right Quantity
Ensuring the correct quantity of products is crucial for balancing supply and demand. Accurate demand forecasting prevents overproduction, which can lead to excess inventory costs and waste, as well as underproduction, resulting in stockouts and lost sales. Advanced inventory management systems and just-in-time (JIT) production methods help maintain optimal inventory levels, guaranteeing customers receive the exact amount of product they need. This balance is vital to avoid unnecessary expenses and keep costs low.
One key element of strategic warehousing is ensuring that inventories meet the expected demand. By doing so, businesses can make important decisions about their supply management.
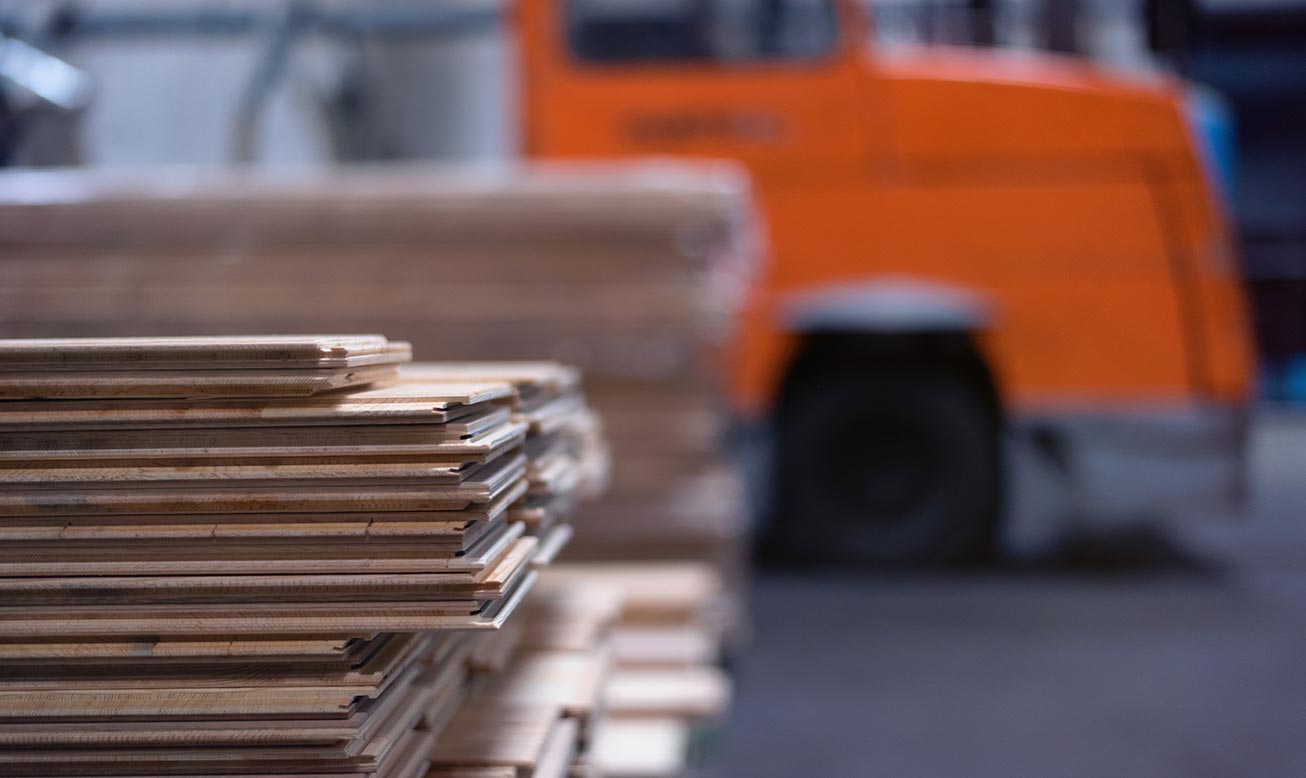
The Right Condition
Maintaining the proper condition of products throughout the supply chain is essential. Goods must be stored and transported in environments that preserve their quality. Effective warehousing solutions, such as climate-controlled storage for perishable goods, ensure products remain in optimal condition. Strategic warehousing also allows for better inventory management and quicker response times to market demands, enhancing overall logistics efficiency.
In addition, white glove services are ideal for ensuring the safe delivery of high-value or delicate goods, whether to manufacturing facilities, retail stores, or end consumers.
The Right Place
Knowing the right place at every stage of the delivery process is crucial. This involves tracking goods from the point of origin to the final destination. Advanced tracking systems and real-time visibility tools enable companies and customers to monitor the location of products throughout the supply chain. Technologies like GPS and RFID tags provide detailed information about the movement and status of goods, ensuring they are in the right place at the right time and enhancing transparency and accountability.
Forward stocking involves storing inventory close to the customer base to ensure quick delivery. This strategy reduces lead time and transportation costs, improving service levels and customer satisfaction. Many businesses, mainly retailers, utilize forward stocking to meet the growing demand for fast delivery, ensuring that products are readily available for customers.
The Right Time
Timing is everything in logistics. Delivering products at the right time involves coordinating various supply chain elements, from production schedules to transportation routes. Effectively managing delivery times, especially across different time zones, prevents delays and enhances customer satisfaction. Expedited shipping services and efficient route planning are essential strategies to ensure timely deliveries, meet customer expectations, and reduce potential disruptions.
Expedited shipping options cater to customers needing quick delivery, often within the same day or overnight. This service requires a well-coordinated logistics network and strategic partnerships with fast transportation services. A recent PwC survey shows that almost 90% of consumers are willing to pay more for same-day or quicker deliveries.
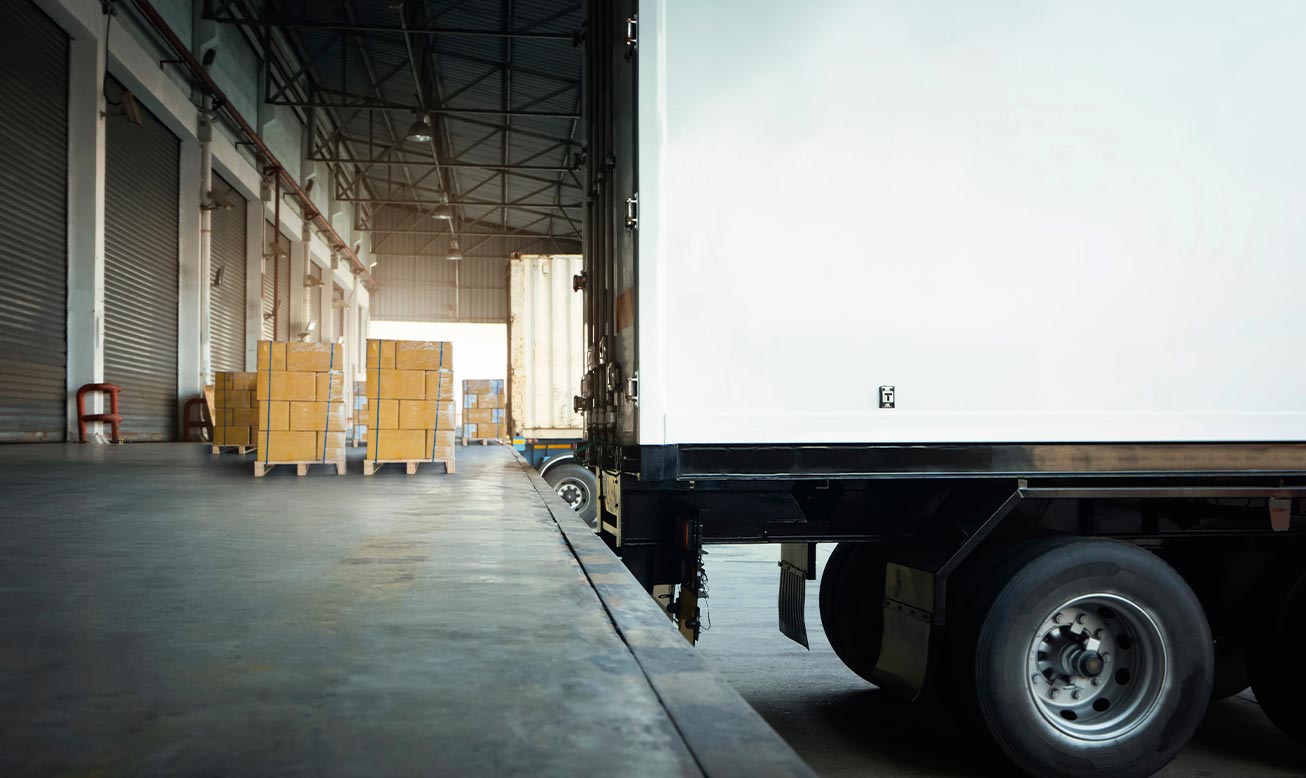
The Right Price
Balancing cost efficiency with quality service is a significant challenge in logistics. The right price includes all expenses involved in the supply chain, including transportation, storage, fuel, tracking systems, and maintenance. Companies must consider these costs to achieve a favorable return on investment (ROI).
Implementing cost-saving measures, such as optimizing routes and consolidating shipments, helps maintain competitive pricing while ensuring high service standards. According to several reports, logistics costs can represent up to 12% of total revenues for companies, which can directly impact the product’s final price, highlighting the relevance of cost management in logistics.
The Right Customer
It is vital to understand customer needs and expectations to provide exceptional service. The right customer involves tailoring logistics solutions to meet specific requirements, whether domestic or international shipping, specialized handling, or expedited shipping. Advanced customer relationship management (CRM) systems help identify and cater to these needs, enhancing customer loyalty and satisfaction. Meeting these expectations improves service quality and builds long-term relationships with customers.
However, end customers can always have a say regarding product satisfaction. Efficient returns management is an essential aspect of logistics. Reverse logistics refers to the process of taking freight from the client’s store back to the manufacturer or warehouse. This process includes handling returns, recycling, refurbishing, and disposal. As over 65% of consumers check the return policy before making a purchase, an efficient reverse logistics process can reduce costs and improve customer satisfaction.
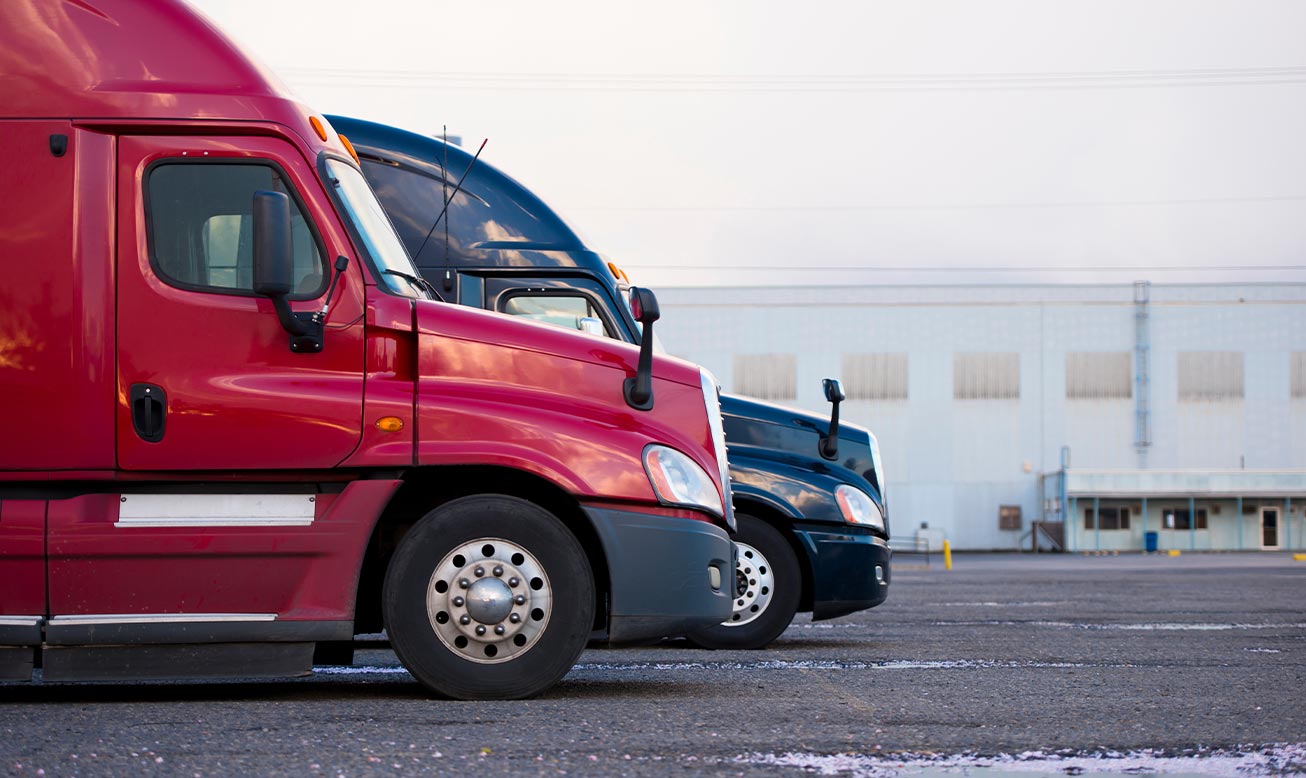
The Importance of the 7 R’s in Logistics
Implementing the 7 R’s of logistics is crucial for any company looking to optimize its supply chain because of the following factors:
Efficiency – Streamlining logistics processes reduces waste and enhances productivity.
Customer Satisfaction – Timely and accurate deliveries improve customer experience and trust.
Cost Savings – Efficient logistics management minimizes operational costs.
Gaining Competitive Advantage – Superior logistics capabilities can set a company apart from its competitors.
Effective vendor management ensures suppliers meet quality and delivery standards when a business seeks significant transportation partnering. Building solid relationships with reliable vendors enhances the overall efficiency of the supply chain. Companies that manage their vendors effectively can ensure a consistent supply of most-needed products, reducing the risk of disruptions.
Additionally, mastering the 7 R’s of logistics is vital for businesses aiming to excel in supply chain management and gain a competitive edge. Whether you are a small business or a large corporation, understanding and applying these principles can significantly impact your success in the market. At Last Mile Logistics, we have the experience and means to manage your freight and logistics requirements, ensuring efficient and reliable delivery services. So please call us so we can evaluate your transportation needs.